Exactly how to Identify What is Porosity in Welding and Improve Your Technique
Exactly how to Identify What is Porosity in Welding and Improve Your Technique
Blog Article
The Scientific Research Behind Porosity: A Comprehensive Guide for Welders and Fabricators
Understanding the detailed systems behind porosity in welding is important for welders and makers pursuing impressive workmanship. As metalworkers dive into the midsts of this phenomenon, they reveal a world controlled by various factors that affect the formation of these tiny voids within welds. From the structure of the base products to the intricacies of the welding procedure itself, a plethora of variables conspire to either intensify or relieve the visibility of porosity. In this comprehensive guide, we will decipher the scientific research behind porosity, discovering its effects on weld quality and introduction advanced techniques for its control. Join us on this journey with the microcosm of welding flaws, where precision satisfies understanding in the quest of perfect welds.
Understanding Porosity in Welding
FIRST SENTENCE:
Exam of porosity in welding reveals vital insights into the stability and top quality of the weld joint. Porosity, defined by the existence of dental caries or spaces within the weld metal, is a typical problem in welding procedures. These spaces, otherwise appropriately attended to, can endanger the structural integrity and mechanical properties of the weld, resulting in possible failures in the ended up item.
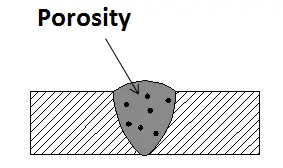
To detect and measure porosity, non-destructive screening methods such as ultrasonic testing or X-ray inspection are often utilized. These techniques permit the recognition of internal issues without compromising the honesty of the weld. By examining the dimension, shape, and distribution of porosity within a weld, welders can make informed choices to enhance their welding processes and attain sounder weld joints.
Aspects Affecting Porosity Formation
The incident of porosity in welding is influenced by a myriad of factors, varying from gas securing efficiency to the details of welding parameter settings. Welding specifications, including voltage, current, take a trip speed, and electrode kind, additionally impact porosity development. The welding method used, such as gas metal arc welding (GMAW) or shielded metal arc welding (SMAW), can affect porosity development due to variations in warmth circulation and gas protection - What is Porosity.
Results of Porosity on Weld Quality
Porosity development significantly endangers the architectural honesty and mechanical residential or commercial properties of bonded joints. When porosity is present in a weld, it develops spaces or cavities within the product, lowering the overall toughness of the joint. These voids work as stress and anxiety concentration factors, making the weld more susceptible to fracturing and failing under lots. The presence of porosity also damages the weld's resistance to deterioration, as the entraped air or gases within deep spaces can react with the surrounding environment, resulting in destruction with time. Additionally, porosity can prevent the weld's capability to endure stress or effect, more endangering the total high quality and dependability of the welded framework. In critical applications such as aerospace, automotive, or architectural constructions, where safety and security and resilience are paramount, the detrimental results of porosity on weld click here to read high quality can have serious effects, emphasizing the value of reducing porosity through correct welding techniques and procedures.
Techniques to Minimize Porosity
Additionally, utilizing the proper welding parameters, such as the appropriate voltage, current, and travel rate, is critical in protecting against porosity. Maintaining a constant arc size and angle during welding also assists reduce the likelihood of porosity.

Utilizing the appropriate welding technique, such as back-stepping or using a weaving motion, can also assist distribute warmth evenly and lower the opportunities of porosity development. By executing these methods, welders can efficiently reduce porosity and create premium welded joints.

Advanced Solutions for Porosity Control
Implementing innovative modern technologies and cutting-edge techniques plays an essential role in attaining remarkable control over porosity in welding processes. One sophisticated option is the usage of sophisticated gas combinations. Protecting gases like helium or a combination of argon and hydrogen can help in reducing porosity by supplying far better arc stability and boosted gas coverage. Additionally, utilizing sophisticated welding strategies such as directory pulsed MIG welding or changed atmosphere welding can likewise aid minimize porosity concerns.
Another innovative option includes using innovative welding tools. For example, using devices with integrated functions like waveform control and sophisticated power sources can boost weld top quality and reduce porosity risks. Additionally, the application of automated welding systems with precise control over parameters can significantly minimize porosity problems.
In addition, incorporating advanced monitoring and assessment innovations such as real-time X-ray imaging or automated ultrasonic screening can assist in spotting porosity early in the welding procedure, permitting prompt restorative actions. On the whole, integrating these sophisticated services her latest blog can greatly improve porosity control and improve the overall quality of welded parts.
Final Thought
In verdict, comprehending the science behind porosity in welding is crucial for welders and fabricators to create top notch welds. By recognizing the aspects affecting porosity formation and implementing techniques to minimize it, welders can improve the overall weld high quality. Advanced options for porosity control can even more enhance the welding procedure and guarantee a solid and trustworthy weld. It is necessary for welders to constantly inform themselves on porosity and carry out best techniques to achieve ideal outcomes.
Report this page